
Pour pouvoir accélérer l’adoption des véhicules électriques dans le monde entier, les bornes de recharge doivent être sûres et fiables. C’est la raison pour laquelle ChargePoint a réalisé d’importants investissements dans des tests de qualité et de fiabilité du matériel. Nous vous proposons ici un aperçu de notre centre de test interne de 1486 mètres carrés !
Le centre de test avancé de ChargePoint établit une nouvelle référence en matière de développement de produits compétitifs dans le secteur de la recharge électrique. Une suite complète de tests y sont réalisés, parmi lesquels des tests de contrainte mécanique, environnementale et opérationnelle effectués sur les sous-systèmes et les bornes de recharge entièrement assemblées. Les ressources de test haute capacité du laboratoire, notamment les dispositifs de test mécaniques, les testeurs de cycle, les chambres thermiques, un testeur de pluie par pulvérisation et de grandes quantités de puissance, permettent de tester de manière contrôlée des échantillons de tailles significatives sur le plan statistique. Nous testons la phase d’introduction du nouveau produit (NPI) et la phase en continu (ORT) jusqu’à la fin de vie du produit (EOL) afin de nous assurer que notre matériel est aussi fiable que possible et que ce niveau de fiabilité est maintenu tout au long du cycle de vie du produit. Ces tests permettent également d’évaluer les risques liés à la conception, aux matériaux et à la fabrication et d’atténuer ces risques lors d’itérations de conception ultérieures.
Tests mécaniques
Nos bornes de recharge ont été conçues et intégrées pour résister aux impacts, aux vibrations, aux chocs, aux chutes et à l’usure cyclique à long terme. Lors de ces tests mécaniques, toutes les parties critiques du système sont testées mécaniquement, comme elles le seraient sur le terrain.
Tests relatifs aux impacts
Une configuration pendulaire a un impact sur l’unité à un niveau d’énergie contrôlé, simulant des circonstances réelles telles que la projection d’une pierre ou un passant qui tenterait d’endommager l’unité. Chaque produit est testé jusqu’à une résistance aux impacts appropriée, le CPE250 étant le plus élevé à IK10 (le classement standardisé le plus élevé).
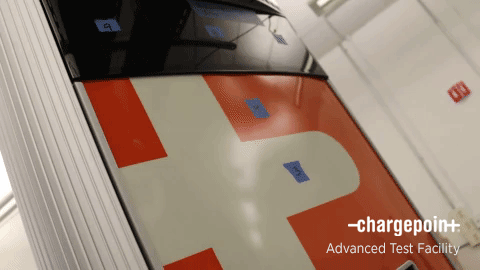
Tests relatifs aux vibrations et aux chutes
Des vibrations appliquées par un système d’agitateur hydraulique à un système opérationnel non emballé simulent les contraintes subies pendant des secousses sismiques, tandis que des vibrations appliquées à une unité entièrement emballée simulent les contraintes subies pendant le transport. Le premier test s’intéresse plus à la sécurité à la suite d’une secousse sismique, tandis que le second aide à évaluer les risques liés au transport afin de maintenir le bon fonctionnement de l’unité à l’arrivée après chaque expédition. Sur le même principe, le produit entièrement emballé subit également des tests relatifs aux chutes.

Cyclage et chargement du système de bras pivotants
Pour recréer les forces de traction potentielles lors de la manipulation, des itérations de traction sont effectuées sur chaque câble du produit à des forces et dans des directions contrôlées (définies via des études utilisateur). Nous allons encore plus loin et effectuons également des itérations de charge statique à force élevée et de choc afin de recréer des scénarios impliquant une manipulation agressive ou une utilisation abusive.
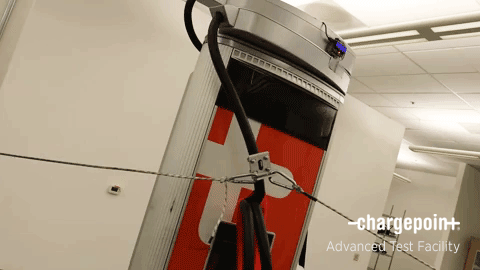
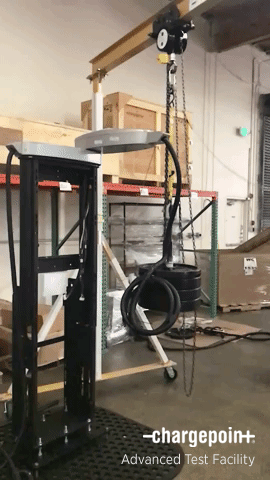
Cyclage du connecteur
Le cyclage des connecteurs de borne de recharge dans les entrées et les supports est automatisé par des testeurs internes sur mesure. Avec ce test, nous évaluons les risques associés à l’accumulation d’usure mécanique (défaillance potentielle due aux interférences des boîtiers de connecteur, des verrous et/ou des contacts électriques).
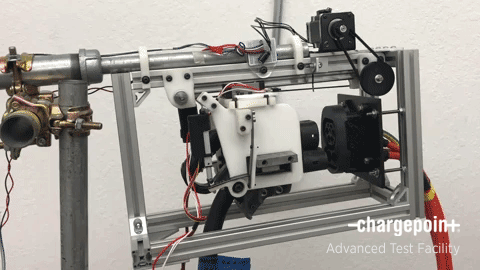
Tests environnementaux
Les tests environnementaux impliquent d’exposer les unités à des conditions atmosphériques extrêmes pendant des périodes prolongées pour s’assurer qu’elles conservent leur fonctionnalité après y avoir été exposées.
Cyclage thermique et de température/d’humidité
Des séjours prolongés à des températures allant jusqu’à 85 °C et des niveaux d’humidité relative (HR) pouvant atteindre 85 % HR exercent une contrainte sur les composants électriques et les matériaux du système sensibles à la corrosion ou à la dégradation due à la chaleur/à l’humidité. Un autre profil de test fait varier la température de -40 °C à 85 °C (avec humidité non contrôlée) pour exercer une contrainte sur les interfaces de liaison et d’intégration des composants internes qui présentent des discordances de coefficient de dilatation thermique (CTE). Cela inclut des pièces du système aussi petites que des joints de soudure sur des PCBA ou des zones plus étendues composées d’adhésifs et de boulons qui relient les cadres et les extrusions.
À partir de là, les profils d’humidité variables forcent la condensation cyclique sur les surfaces externes et internes, simulant la formation de rosée dans les climats humides. Ce profil de contrainte est ensuite exacerbé par des conditions de chambre modifiées qui forcent cette condensation à geler (lorsque l’eau se transforme en glace au niveau des interstices du système et sur les surfaces des composants).
Les tests de température et d’humidité décrits ci-dessus mettent nos produits à l’épreuve pendant et au-delà de leur durée d’exposition prévue.
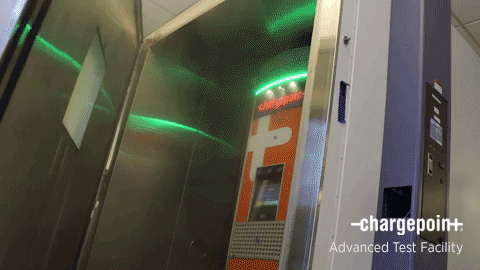
Tests de pulvérisation, de poussière et de brouillard salin
Les tests de pulvérisation permettent de simuler des scénarios de pluie et de lavage sous pression. Les tests de poussière dans le désert simulent une accumulation prolongée de particules conductrices. Les tests de brouillard salin simulent une corrosion accélérée dans les régions côtières.
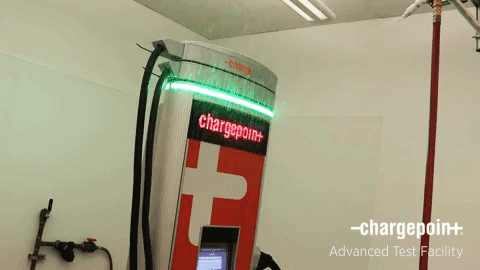
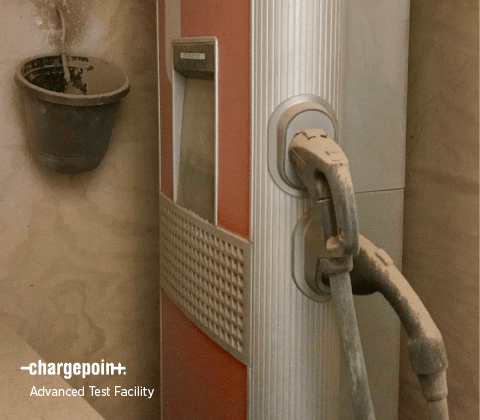
Tests de charge solaire et d’exposition aux UV
Les produits sont exposés à un ensemble complet de tests de photodégradation due à l’énergie solaire, de résistance à la lumière, de charge thermique et de stabilité aux UV pour tester leur fonctionnement permanent. La disposition de plusieurs lampes haute puissance dans une zone fermée permet d’obtenir la gamme complète du spectre du soleil afin de simuler la charge solaire, tandis qu’une chambre séparée concentre les rayons UVA sur les unités de test.
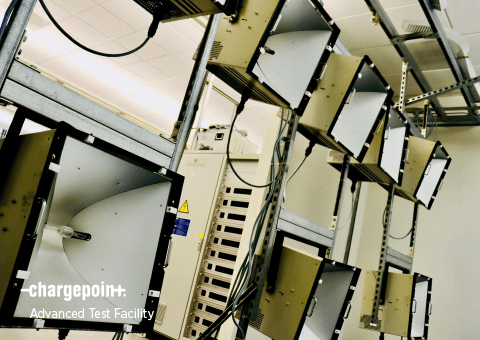
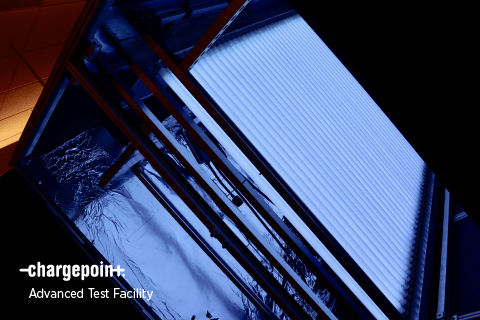
Tests de contrainte opérationnelle
Sans doute la catégorie de tests la plus importante, les tests de contrainte opérationnelle à long terme font travailler toutes les fonctions essentielles du système dans des conditions extrêmes. Cela nécessite une automatisation basée sur Python et/ou BASH qui accélère les opérations du produit afin de simuler l’utilisation sur le terrain tout au long de son cycle de vie prévu.
Ce test est ensuite effectué avec l’unité dans un environnement surélevé à 50 °C afin de solliciter le mécanisme de gestion thermique du système. Ce test intègre également un simulateur de véhicule électrique, effectuant une opération de bout en bout qui simule les cycles de recharge effectués par les véhicules sur le terrain. Pendant ce temps, les fonctions secondaires du système (telles que les sorties d’affichage, l’éclairage LED et même les haut-parleurs émettant un signal sonore) émettent des cycles de sortie dans des conditions de contrainte maximale.
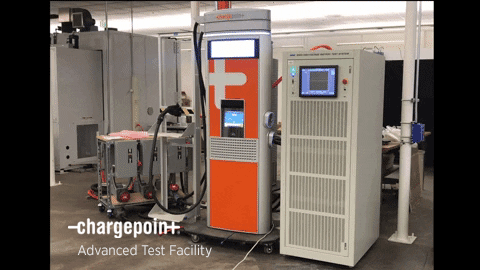
Difficultés lors du test du système
Les tests effectués au centre de test avancé de ChargePoint permettent à nos équipes d’ingénieurs interfonctionnelles de développer des produits sûrs et fiables malgré les contraintes mécaniques, environnementales et opérationnelles intenses qu’ils peuvent subir sur le terrain au cours de leur cycle de vie prévu. Les risques identifiés par les tests sont évalués en fonction de leur gravité, de leur détectabilité et de leur probabilité à déterminer l’impact attendu sur l’utilisateur, ce qui permet ensuite de définir un calendrier approprié pour atténuer le problème.
Avec ce centre de test dernier cri, qui a coûté des millions de livres, nous montrons clairement notre engagement envers l’intégrité des produits. En investissant dans des tests internes, nous sommes en mesure de réaliser un plus large éventail de tests et d’obtenir plus facilement, pour chaque test, des résultats significatifs sur le plan statistique. Les fournisseurs qui choisissent de confier les tests à des laboratoires tiers (à des fins de réduction des coûts) ne peuvent tout simplement pas en dire autant.
Notre centre de test continue à évoluer avec de nouveaux équipements. Cette année, nous avons ajouté un système de vibrations hydrauliques à charge élevée, une chambre à poussière et une chambre à brouillard salin. Les ressources de notre site, associées à nos objectifs de produits de plus en plus ambitieux, favorisent un environnement de test de système qu’il est difficile de trouver ailleurs.
Découvrez notre centre de test interne comme si vous y étiez :